3 Simple Techniques For Alcast Company
Table of ContentsThe smart Trick of Alcast Company That Nobody is DiscussingSome Known Facts About Alcast Company.Alcast Company - QuestionsThe Best Strategy To Use For Alcast CompanyNot known Incorrect Statements About Alcast Company The Single Strategy To Use For Alcast Company
The subtle difference depends on the chemical content. Chemical Comparison of Cast Aluminum Alloys Silicon promotes castability by minimizing the alloy's melting temperature level and improving fluidity throughout spreading. It plays a critical function in enabling detailed mold and mildews to be filled accurately. Additionally, silicon adds to the alloy's toughness and put on resistance, making it valuable in applications where durability is crucial, such as automobile parts and engine components.It also improves the machinability of the alloy, making it much easier to refine right into completed items. This way, iron contributes to the overall workability of aluminum alloys. Copper raises electric conductivity, making it beneficial in electric applications. It likewise boosts deterioration resistance and contributes to the alloy's total strength.
Manganese adds to the stamina of light weight aluminum alloys and enhances workability. Magnesium is a lightweight component that gives toughness and influence resistance to light weight aluminum alloys.
The smart Trick of Alcast Company That Nobody is Discussing
It enables the production of lightweight components with superb mechanical residential or commercial properties. Zinc improves the castability of light weight aluminum alloys and aids control the solidification process during spreading. It boosts the alloy's strength and solidity. It is typically located in applications where detailed forms and fine details are required, such as attractive spreadings and specific auto components.
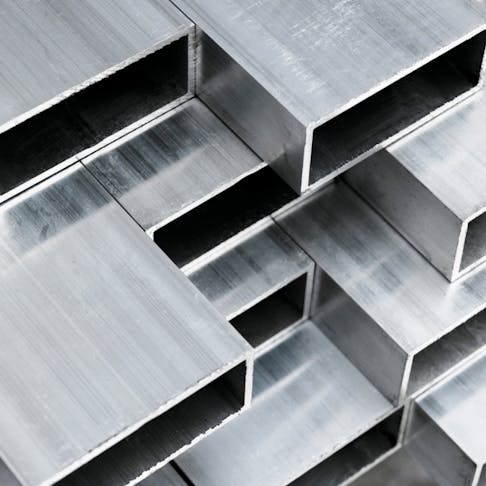
The key thermal conductivity, tensile strength, yield stamina, and prolongation differ. Select suitable raw materials according to the performance of the target item generated. Among the above alloys, A356 has the greatest thermal conductivity, and A380 and ADC12 have the cheapest. The tensile limit is the contrary. A360 has the most effective return stamina and the greatest elongation price.
Alcast Company Things To Know Before You Buy

In accuracy casting, 6063 is fit for applications where elaborate geometries and high-quality surface area coatings are critical. Instances consist of telecommunication units, where the alloy's exceptional formability permits for sleek and cosmetically pleasing designs while preserving architectural integrity. In the Illumination Solutions market, precision-cast 6063 elements develop elegant and efficient illumination components that need complex shapes and great thermal efficiency.
It leads to a finer surface area finish and better rust resistance in A360. The A360 exhibits superior prolongation, making it perfect for complicated and thin-walled elements. In precision casting applications, A360 is well-suited for industries such as Consumer Electronic Devices, Telecommunication, and Power Devices. Its boosted fluidness permits elaborate, high-precision parts like smart device coverings and communication gadget housings.
The Ultimate Guide To Alcast Company
Its special residential or commercial properties make A360 a useful option for accuracy spreading in these industries, improving item longevity and quality. Light weight aluminum alloy 380, or A380, is an extensively made use of casting alloy with numerous distinctive attributes. It supplies outstanding castability, making it an excellent choice for accuracy spreading. A380 shows great fluidness when molten, making certain detailed and detailed molds are accurately duplicated.
In precision casting, aluminum 413 radiates in the Consumer Electronic Devices and Power Equipment industries. This alloy's superior rust resistance makes it an outstanding option for outdoor applications, making certain resilient, long lasting items in the mentioned industries.
The Best Strategy To Use For Alcast Company
As soon as you have determined that the aluminum pass away casting process is ideal for your project, a crucial following action is selecting one of the most suitable alloy. The aluminum alloy you select will substantially influence both the casting procedure and the buildings of the end product. As a result of this, you need to make your choice carefully and take an enlightened method.
Figuring out one of the most appropriate aluminum alloy for your application will mean evaluating a large variety of features. These relative alloy qualities comply with the North American Die Casting Organization's guidelines, and we've split them into 2 categories. The first category addresses alloy characteristics that influence the production procedure. The second covers attributes influencing the properties of the end product.
How Alcast Company can Save You Time, Stress, and Money.
The alloy you choose for die spreading directly impacts a number of aspects of the spreading process, like just how simple the alloy is to work with and if it is vulnerable to casting defects. go to this site Warm splitting, also understood as solidification cracking, is a common die spreading flaw for aluminum alloys that can cause inner or surface-level rips or cracks.
Certain aluminum alloys are extra susceptible to warm fracturing than others, and your option needs to consider this. It can damage both the actors and the die, so you ought to look for alloys with high anti-soldering buildings.
Deterioration resistance, which is already a noteworthy feature of light weight aluminum, can vary substantially from alloy to alloy and is a crucial particular to think about depending upon the environmental problems your item will be subjected to (Casting Foundry). Use resistance is another home generally sought in aluminum products and can set apart some alloys